提升橡胶密封件在化工设备中的抗腐蚀能力,可从材料选择、表面处理、结构设计、安装使用等方面着手,具体方法如下:
选择合适的橡胶材料
耐腐蚀性橡胶:根据化工设备中接触的化学介质选择相应的耐腐蚀性橡胶材料。例如,丁腈橡胶具有良好的耐油性,适用于接触油类介质的化工设备;氟橡胶对强氧化剂、强酸、强碱等具有优异的耐腐蚀性,常用于化工腐蚀环境较为恶劣的场合;乙丙橡胶则具有突出的耐水性和耐水蒸气性能,适合在有水分或水蒸气存在的化工环境中使用。
添加防老剂和抑制剂:在橡胶配方中加入适量的防老剂和腐蚀抑制剂,可以提高橡胶的抗氧化和抗腐蚀能力。防老剂能够抑制橡胶在使用过程中的老化降解,保持橡胶的性能稳定;腐蚀抑制剂可以在橡胶表面形成一层保护膜,阻止化学介质与橡胶发生反应,从而提高橡胶密封件的抗腐蚀能力。
优化密封件表面处理
涂层保护:采用喷涂、浸渍等方法在橡胶密封件表面涂覆一层耐腐蚀的涂层,如聚四氟乙烯涂层、陶瓷涂层等。这些涂层具有良好的化学稳定性和低摩擦系数,能够有效地隔离橡胶与化学介质的接触,减少腐蚀的发生,同时还能降低密封件与设备表面的摩擦,提高密封件的使用寿命。
表面改性:通过化学或物理方法对橡胶密封件表面进行改性处理,如等离子体处理、紫外线照射等。这些处理方法可以改变橡胶表面的化学结构和性能,提高表面的硬度、粗糙度和耐腐蚀性,增强橡胶密封件与化学介质的接触角,使化学介质难以在密封件表面附着和渗透,从而提高抗腐蚀能力。
改进密封件结构设计
合理设计密封形式:根据化工设备的工作条件和密封要求,选择合适的密封形式。例如,对于压力较高、腐蚀性较强的化工介质,可以采用多道密封结构,如采用唇形密封与 O 形圈密封相结合的方式,增加密封的可靠性,减少介质泄漏的可能性,从而降低腐蚀的风险。
优化密封件尺寸:确保密封件的尺寸与化工设备的安装部位精确匹配,避免因尺寸不当导致密封件在使用过程中出现过度变形或应力集中的现象。合理的尺寸设计可以使密封件在工作状态下保持良好的密封性能,减少因密封不严而导致的化学介质泄漏,进而提高抗腐蚀能力。
正确安装与使用维护
正确安装:在安装橡胶密封件时,应严格按照安装说明书进行操作,避免密封件受到损伤或扭曲。安装过程中要确保密封件表面清洁,无杂质、油污等,防止这些物质对密封件造成腐蚀或影响密封性能。同时,要注意安装的力度和方法,避免因安装不当导致密封件产生裂纹或变形,从而降低其抗腐蚀能力。
定期维护与更换:制定定期检查和维护的计划,及时发现橡胶密封件的磨损、老化和腐蚀情况。对于已经出现损坏或性能下降的密封件,应及时进行更换,以防止化学介质泄漏引发更严重的腐蚀问题。此外,还应注意对化工设备进行整体的维护保养,保持设备的清洁和正常运行,减少因设备故障而对密封件造成的不良影响。
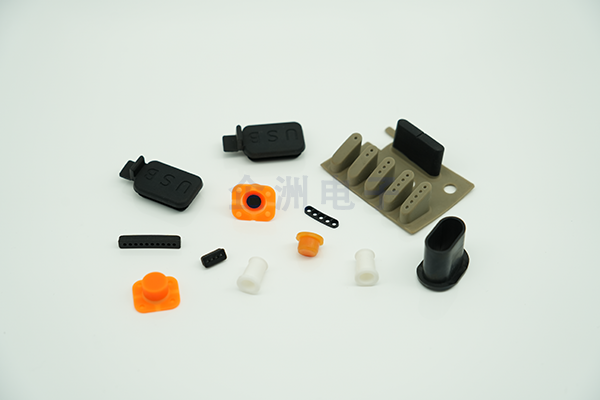