密封橡胶件的硬度稳定性会受到多种因素的影响,包括橡胶的配方、加工工艺、使用环境及老化等方面,具体如下:
橡胶配方
生胶种类:不同种类的生胶具有不同的分子结构和性能,会影响橡胶件的硬度。例如,天然橡胶分子链柔顺性好,硫化后硬度相对较低;而丁腈橡胶由于含有极性腈基,分子间作用力较大,硫化后硬度较高。
填充剂:填充剂的种类和用量对橡胶硬度影响显著。如炭黑、白炭黑等填充剂,加入量越多,橡胶的硬度越高。这是因为填充剂粒子分散在橡胶基体中,增加了橡胶的刚性。
增塑剂:增塑剂的作用是降低橡胶分子间的作用力,增加橡胶的柔韧性和可塑性。加入增塑剂会使橡胶硬度降低,且随着增塑剂用量的增加,硬度下降幅度增大。
加工工艺
硫化温度:硫化温度过高,会使橡胶分子交联速度加快,交联密度增大,导致橡胶硬度增加。反之,硫化温度过低,交联反应不完全,橡胶硬度会偏低。
硫化时间:硫化时间延长,橡胶的交联程度增加,硬度也会随之提高。但当硫化时间达到一定程度后,交联反应基本完成,继续延长时间对硬度的影响就不明显了。
混炼工艺:混炼过程中,若混炼不均匀,橡胶中的各种配合剂分布不均,会导致橡胶硬度出现局部差异。同时,混炼时间过长或过短都会影响配合剂与橡胶的结合程度,进而影响硬度稳定性。
使用环境
温度:温度升高,橡胶分子热运动加剧,分子间作用力减弱,橡胶硬度会降低;温度降低,分子热运动减缓,分子间作用力增强,硬度则会升高。而且长期处于高温环境下,橡胶还可能发生热老化,导致硬度发生不可逆的变化。
介质:橡胶密封件在使用过程中若接触到油类、酸碱等化学介质,可能会发生溶胀或腐蚀。溶胀会使橡胶分子链间距增大,硬度降低;腐蚀则会破坏橡胶的分子结构,导致硬度变化。
压力:在高压作用下,橡胶密封件会发生压缩变形,内部结构被压缩,分子间距离减小,硬度会有所增加。当压力消除后,橡胶若不能完全恢复原状,会产生永久变形,也会影响硬度的稳定性。
老化因素
氧化:橡胶与空气中的氧气发生氧化反应,会使橡胶分子链断裂或产生交联,导致橡胶硬度发生变化。一般来说,氧化初期,橡胶分子链断裂占主导,硬度会降低;随着氧化程度加深,交联反应逐渐增强,硬度又会升高。
臭氧:臭氧会与橡胶分子中的双键发生反应,生成臭氧化物,使橡胶表面产生裂纹,破坏橡胶的结构,从而影响硬度。
光辐射:紫外线等光辐射会引发橡胶分子的光化学反应,加速橡胶的老化,导致硬度改变。同时,光辐射还可能使橡胶中的增塑剂等添加剂分解或挥发,进一步影响硬度稳定性。
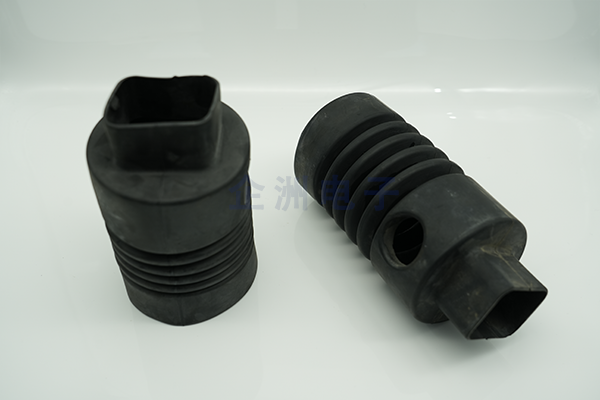