密封橡胶件的硬度是一项重要的性能指标,对其使用寿命有着显著影响,具体如下:
硬度对密封性能的影响
硬度较低:橡胶件容易发生变形,能更好地适应密封表面的不平整,填充微小间隙,从而提供良好的初始密封效果。然而,在长期使用中,特别是在承受较高压力时,低硬度的橡胶件可能会因过度变形而被挤出密封间隙,导致密封失效,缩短使用寿命。例如,在一些高压管道密封中,若橡胶密封件硬度太低,可能在短时间内就会出现泄漏现象。
硬度较高:橡胶件较难发生变形,在受到压力时能保持较好的形状,不易被挤出。但如果硬度过高,橡胶件与密封表面的贴合性会变差,难以填充微小的凹凸不平,容易出现密封不严的情况,使介质泄漏,影响其使用寿命。比如在一些需要高精度密封的机械部件中,硬度过高的橡胶密封件可能无法实现良好的密封,导致设备故障。
硬度对磨损和疲劳性能的影响
硬度较低:橡胶的弹性较好,能吸收一定的冲击力和振动,在相对运动的密封部位,可减少因摩擦和冲击引起的磨损。不过,长期反复的变形容易使低硬度橡胶产生疲劳,出现内部裂纹和损伤,进而降低其使用寿命。例如在汽车发动机的一些密封部位,低硬度橡胶密封件在长时间使用后可能会因疲劳而出现泄漏。
硬度较高:橡胶的刚性较大,耐磨性能较好,在受到摩擦和磨损时,表面不易被划伤和磨损。但高硬度橡胶在受到外力作用时,内部应力集中现象较为明显,容易在应力集中处产生裂纹,尤其是在频繁的动态载荷作用下,疲劳寿命会显著降低。例如在一些高速旋转的机械密封中,硬度过高的橡胶密封件可能会因疲劳裂纹的快速扩展而失效。
硬度对老化性能的影响
硬度较低:通常含有较多的增塑剂等添加剂,这些添加剂在长期使用过程中可能会逐渐迁移或挥发,导致橡胶变硬、变脆,加速老化。而且低硬度橡胶的分子链活动性相对较高,更容易受到外界因素如氧气、臭氧、热等的影响,发生氧化、交联等反应,缩短使用寿命。
硬度较高:一般交联密度较大,分子链间的结合较为紧密,对氧气、臭氧等老化因素的抵抗能力较强。但硬度过高可能会使橡胶的韧性降低,在老化过程中更容易出现裂纹,一旦裂纹产生,会加速橡胶的破坏,影响其使用寿命。
在实际应用中,需要根据密封橡胶件的具体使用环境和要求,合理调整其硬度,以达到最佳的密封效果和最长的使用寿命。例如,在高温、高压且相对运动速度较低的环境中,可适当提高橡胶件的硬度;而在一些动态密封且要求良好柔韧性的场合,则应选择硬度较低的橡胶件,并通过优化配方和结构设计来提高其耐疲劳性能和使用寿命。
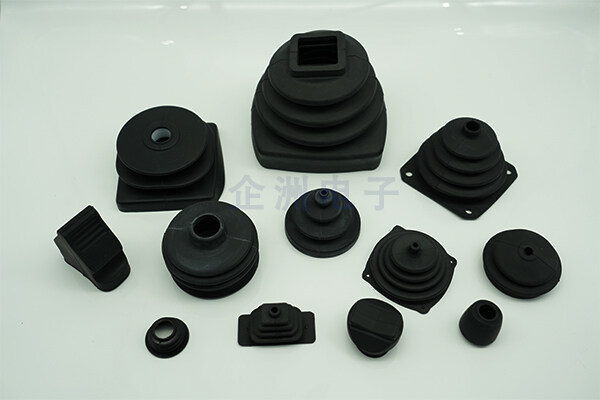