要保证橡胶密封件的尺寸精度,需要在模具设计制造、原材料选择、生产工艺控制以及质量检测等环节采取一系列措施,具体如下:
模具设计与制造
精确设计:根据橡胶密封件的尺寸要求进行精确的模具设计,考虑橡胶材料的收缩率、成型工艺等因素,通过计算机辅助设计(CAD)等软件进行模拟分析,优化模具结构,确保模具尺寸能够准确反映密封件的最终尺寸要求。
制造精度:采用高精度的加工设备和先进的加工工艺来制造模具,如数控加工中心、电火花加工等,保证模具的加工精度在微米级别,严格控制模具的尺寸公差,以确保模具型腔的尺寸精度符合设计要求。
模具维护:定期对模具进行清洁、保养和维修,检查模具的磨损情况,及时更换磨损的部件,确保模具的精度长期稳定。
原材料选择
生产工艺控制
成型工艺参数优化:对于模压成型、注射成型等不同的成型工艺,要精确控制工艺参数,如温度、压力、时间等。通过实验和数据分析,确定最佳的工艺参数组合,以保证橡胶在成型过程中能够均匀流动、充分硫化,从而获得尺寸稳定的密封件。
硫化过程控制:硫化是橡胶密封件生产中的关键环节,要严格控制硫化温度和时间,确保橡胶充分硫化且硫化程度均匀。采用先进的硫化设备,如平板硫化机、注射硫化机等,并配备精确的温度控制系统和计时装置,以保证硫化过程的稳定性和重复性。
生产环境控制:保持生产环境的温度、湿度稳定,避免环境因素对橡胶材料和成型过程产生影响。一般来说,生产环境温度应控制在 25℃±5℃,相对湿度控制在 40% - 60% 为宜。
质量检测与控制
首件检验:在生产批次开始时,对首件产品进行全面的尺寸检测和性能测试,确保产品符合设计要求。如发现尺寸偏差,及时分析原因并调整模具或工艺参数,直至首件产品合格后方可进行批量生产。
过程检验:在生产过程中,定期对产品进行抽样检测,采用量具如卡尺、千分尺、三坐标测量仪等对密封件的关键尺寸进行测量,及时发现尺寸波动并采取措施进行调整。同时,对产品的外观质量、硬度、拉伸强度等性能指标进行检验,确保产品质量稳定。
成品检验:对生产完成的橡胶密封件进行 100% 的尺寸和性能检验,剔除不合格产品。建立质量追溯体系,对每一件产品的生产过程和质量数据进行记录,以便在出现问题时能够及时追溯和分析原因。
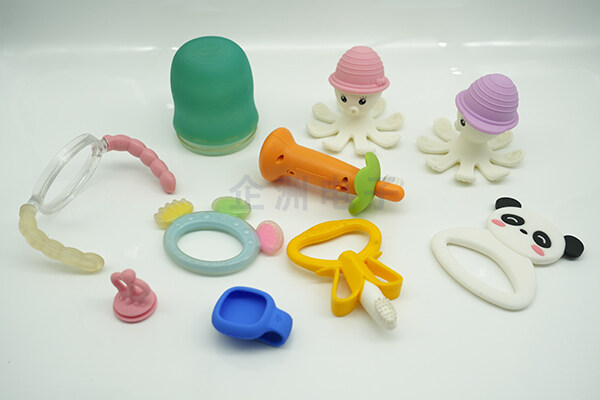