为提高硅胶密封圈的耐候性,可从原材料选择、优化加工工艺、产品设计改进及后期处理与维护等方面着手,具体方法如下:
原材料选择
加工工艺优化
精确硫化参数:严格控制硫化温度、时间和压力。一般来说,硫化温度在 150℃-200℃之间,硫化时间根据产品厚度和配方不同,在 10-60 分钟范围内调整,确保硅胶分子形成均匀、稳定的交联结构,以提高产品的物理性能和耐候性。
改善成型工艺:对于模压成型,要保证模具的精度和表面质量,使密封圈成型后尺寸精确、表面光滑,减少因表面缺陷导致的应力集中和老化隐患。对于挤出成型,要优化挤出速度和牵引速度,确保产品的致密度和均匀性。
产品设计改进
优化结构设计:根据使用场景,合理设计密封圈的形状和尺寸,避免出现尖锐的边角和过度的薄厚变化,以减少应力集中。例如,采用圆角过渡代替直角过渡,适当增加密封圈的厚度和宽度,提高其承载能力和抗变形能力。
考虑安装因素:设计时要充分考虑密封圈的安装方式和配合精度,确保安装过程中密封圈不受损伤,且在使用中能均匀受力。例如,设计合理的安装沟槽,使密封圈在安装后既能保证密封效果,又不会因过紧或过松而影响其耐候性。
后期处理与维护
表面处理:对硅胶密封圈进行表面涂层处理或化学处理,可提高其表面性能和耐候性。如采用硅烷偶联剂对密封圈表面进行处理,能增强其表面的耐水性和耐化学腐蚀性;或者涂覆一层耐候性涂料,可有效隔离外界环境对硅胶的影响。
定期维护检查:制定定期检查和维护计划,及时发现密封圈的磨损、老化等问题并进行更换。同时,在使用过程中要避免密封圈接触尖锐物体和腐蚀性物质,防止对其造成损伤。此外,还需根据使用环境和频率,合理确定维护周期,一般建议每 3-6 个月进行一次全面检查和维护。
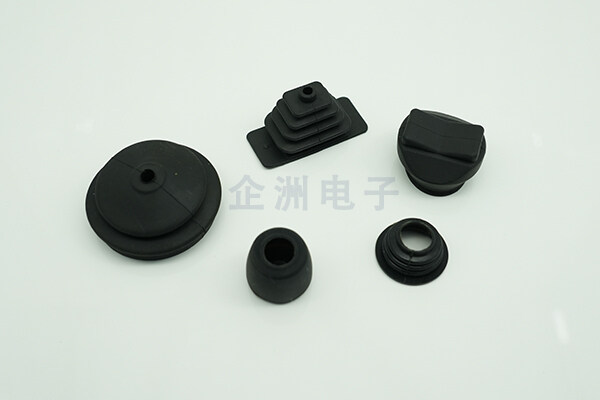